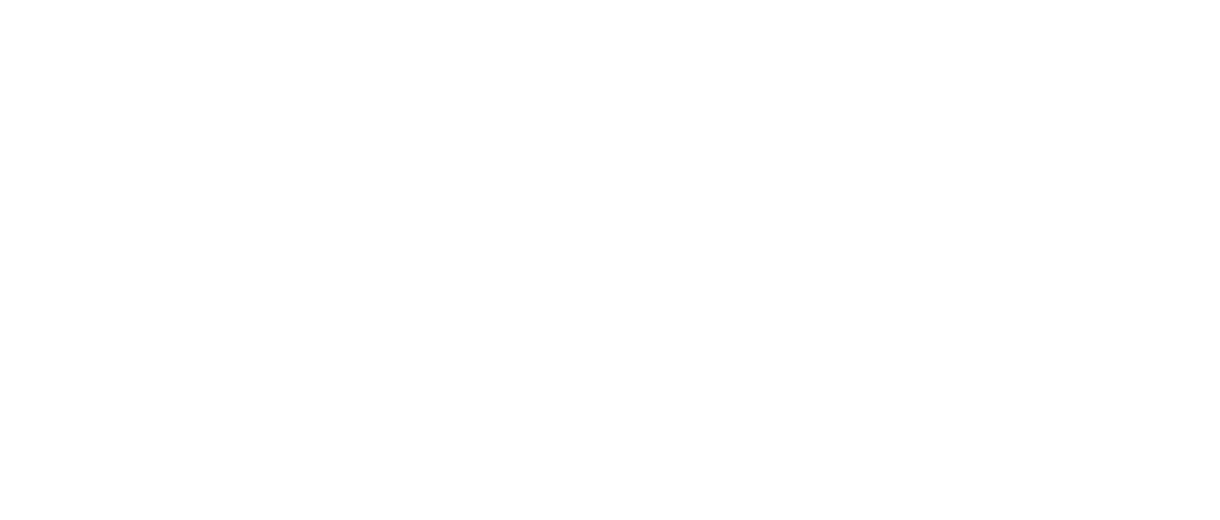
Tip Top Equipment – AVT Oracle NetSuite ERP Implementation Case Study
Tip Top Equipment are a family owned business specialising in after market vehicle modifications including manufacturing of custom products for Utes and Vans. The product range includes Ute Trays, Van Fit-outs, Trundle Trays and more. The configuration of these products can be well over a billion combinations of features and options presented to the customer. There is a wide variety of solutions offered including repairs and warranty on products delivered.
Challenge
- Outgrown paper based systems to run business operations
- Disparate systems for Finance, CRM, Product Configuration, Quoting, Orders Management, Inventory, Warehousing and Production Management.
- Maintain product and services delivery with increase in demand and business growth.
- Accurately budget, forecast and track investment to meet current demand
Needs
- Consolidate systems to provide accurate business reporting
- Systemise configuration and quoting options to improve sales
- Streamline order approval and delivery processing for both cash and credit customers
- Stream delivery of jobs
- Track and Improve business productivity and profitability
- Scale business operations to work at multiple locations within Australia
The AVT Engagement and Solution
AVT was recommended to Tip Top to assist with the business transformation project and provide an in-depth analysis of the issues confronting the business. AVT conducted a series of workshops with the business and systems owners at Tip Top Equipment. AVT’s implementation team provided expertise to assist the Tip Top team in the reworking of processes and procedures to implement Netsuite and AVT NetSuite Modules into the full breadth of business functions including Financials, Sales and CRM, Marketing, Procurement, Inventory Management, Warehousing and Manufacturing.
- AVT worked with Tip Top to develop a product configuration tool that enabled sales staff to step through a simple to use Features and Options process that ensured that only viable combinations were quoted; that they met the customer’s requirements and were correctly priced. The quote form sales sent to the client was formatted to include any configuration details.
- AVT worked with the engineering team to build a “Dynamic” Bill of Materials (BOM) configurator that enabled the update of existing Make to Order configurations on Orders and Quotes in NetSuite without the need of having preconfigured BOMs/SKUs in the system.
- AVT assisted with the payment/work release process by implementing its Present and Pay solution. This provides a link on the invoice PDF that allows the customer to immediately open up a site and process payment electronically. This enables Finance to quickly see that the payment is processed and, with NetSuite being an integrated system, the approval to start production is issued with minutes. This has had a significant impact on the production process.
- AVT Netsuite Inventory, Warehousing and Manufacturing modules were able to provide Tip Top Equipment with accurate usage and replenishment of stock and manufactured products to meet demand.
- Integrated real-time P/L, Job Costing, Dashboards and Business reporting was able to provide Tip Top with accurate metrics and KPIs to drive business performance.