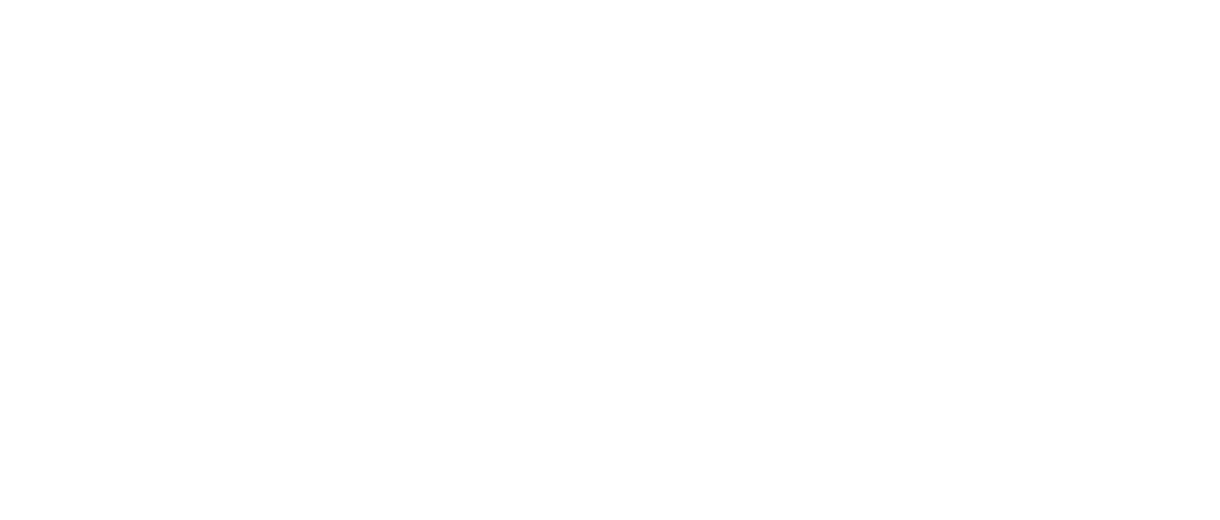
Inventory Management for Distribution and Retail Businesses
Leveraging Integrated Systems: The Key to Streamlined Operations and Enhanced Reporting
Unlock the keys to efficient inventory management with our comprehensive guide. Explore best practices, strategies, and technologies that enable businesses to optimise stock levels, minimize carrying costs, and improve overall supply chain performance. Discover how effective inventory management empowers organizations to meet customer demands, reduce waste, and achieve a competitive edge in today’s dynamic market.
Introduction
Distribution and Retail businesses rely on accurate safety stock and lead time to forecast expected delivery dates and manage customer delivery expectations. With increasing competition and it’s imperative that businesses can manage the delivery exceptions accurately as possible.
The timing of procurement decisions is a crucial decision in ensuring the customers are supplied on time while keeping inventory at optimal working capital levels.
Summary
The questions to be addressed by procurement are:
- What quantity has to be acquired?
- When should the Purchase Order be sent?
- Which vendor should it be sent to?
Determining Quantity
NetSuite provides three critical variables for producing a recommended Quantity to purchase.
- Preferred Stock Level; the optimal quantity of the item to be held in a given Location (Store or Warehouse)
- Reorder Point; the quantity in a given location at which a new order must be placed.
- Available Quantity; the quantity on hand less the quantity committed to orders.
Netsuite is continually monitoring these factors, and then Quantity Available drops below Reorder Point, the item will appear on the Order Items for the Procurement Department.
The quantity to be ordered is Preferred Stock Level – Available Quantity.
Example:
Item ABC, Location: Sydney , Inventory on Hand 500, Inventory Committed 300, Available Quantity 200, Preferred Stock Level 1000, Reorder Point 240
Recommended Order Quantity: 1000 – 200 = 800 units
Determining Timing
Critically for this model, the quantity being ordered must be set so that the order will arrive before the remaining available inventory is consumed.
For this to be achieved, the following must be taken into account:
- Lead Time: the length of time, in days, between placing the order and its expected delivery.
- Safety Stock; the quantity of inventory to be held as the bare minimum required to cover consumption while waiting for an order to be placed and received. This may be stored as a quantity or can be calculated by NetSuite.
- Reorder Point; This is commonly set as a quantity buffer between Preferred Stock Level and Safety Stock. it provides cover for Safety stock for situations such as Vendor delivery issues. this may be stored as a quantity or can be calculated by NetSuite.
- Daily Demand; Netsuite calculates this based on the user-defined length of historical consumption, which is then divided by the number of dates within that length of time e,g last six months’ sales for the location, are a total of 540, which, when divided by 180, would mean daily sales for calculation purposes equals 3. This value is recalculated on a user-defined frequency, most commonly monthly.
These settings are all important to establishing that the correct quantity is recommended at the right time.
Critical Calculations for Lead Time:
1. How do we calculate accurate lead time?
NetSuite calculates lead time based on the previous three Purchase Orders delivered.
It averages the number of days between the Order Date and the Item Received Date and updates the item record for the location concerned.
2. How do we calculate Safety Stock and Reorder Point?
Netsuite provides for both of these quantities to be calculated as a function of the number of days set for each and the Daily demand values.
The following is an example using the data from earlier:
• Example 1 – Safety Stock = 45 days, Average Lead Time 35 days, Average Daily Consumption = 3
Safety Stock Qty = Safety Stock Days * Average Demand (45 * 3 = 135)
Reorder Point Qty = (Safety Stock Days + Average Lead Time) * Average Daily Demand (45+35)*3 = 240
With an Available Inventory of 200 units and average demand of 3, the example has 66 days of consumption cover, comfortably above the Safety Stock level.
A review might decide to cut Safety Stock back by ten days, which would:
- Reduce Safety Stock by 60 Units
- Reduce Reorder Point by 60 units to 180.
- Delay the need for the Purchase to be raised by around 20 days.
- If the item were valued at $100, this would defer the $80,000 Purchase Order by nearly a month, improving the organisation’s Liquidity ratio.
Streamlining Purchase Order Preparation.
NetSuite provides a single screen enabling the relevant user to see all of the recommendations and then be able to convert them into Purchase Orders with a minimum of effort.
Streamlining Distribution to Other Locations
As the Safety, Reorder, and Preferred Stock levels are held at the Location level, the inventory management team can use this data to determine when stock needs to be shipped to these locations.
Using Inventory management features of Oracle NetSuite, distribution companies like SPOS & iCandy Creative, Australian Fitness Supplies, Uniden Australia and Bisley & Company have been able achieve just that. To find out more about how you can implement inventory management, please reach out to AVT – Absolute Vision Technologies (Oracle NetSuite VAR, Partner & SI) at Contact AVT Page and get your inventory management strategy and implementation plan. AVT is committed to help deploying the Inventory management automation for distribution businesses.
New to NetSuite?
With over 32,000 customer globally, over 200 AVT Clients, and increasing, get your personalised ERP transformation Workbook on Oracle NetSuite Evaluation Discovery. Our service and support plans will typically get you live in approx. 90 days and so you may focus on getting your business globally integrated as soon as possible.
Oracle NetSuite ERP System – The #1 Cloud Business Management System
The only ERP you’ll ever need
Oracle NetSuite ERP is a cloud based business platform that provides your business with complete end to end solution and integrated reporting to run your organisation in a streamlined way. With over 32K customers globally, your business can easily deploy and roll out streamlined processes, prebuilt Dashboards, Reports, KPI that can help overcome reporting and operational challenges you are facing today and align your business to meet future needs. Using the APIs, you can easily integrate your ERP data with 3rd Party systems and reduce your data entry administration.
To learn more, AVT – Australia’s Leading NetSuite Solution Provider & Partner has created a complimentary NetSuite ERP Evaluation micro-site to help executives learn more about ERP and its deployment, using pre-recorded process demo videos, White papers and data sheets, so you may evaluate this at your own pace. You can gain access to to the site by completing your Registration in the link: NetSuite Overview Demos.
ERP Resources
One System For Your Entire Company
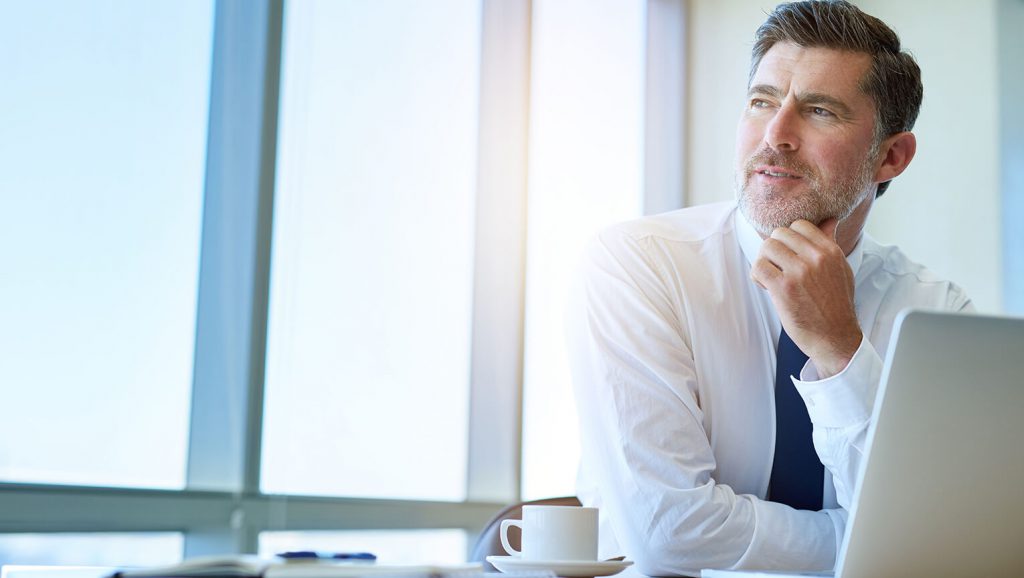
Evaluate
NetSuite ERP
NetSuite ERP
AVT makes your ERP evaluation easier. Using our NetSuite Evaluation workbook, Questionnaires, IT Roadmapping and ROI Analysis tools your organisation can easily develop a business case for an ERP upgrade project.
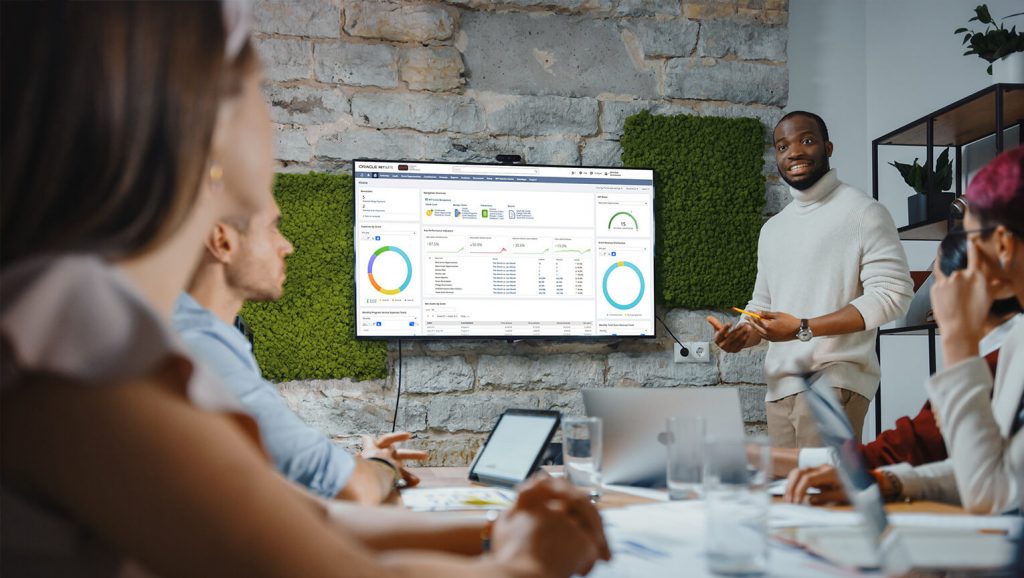
NetSuite ERP
Implementation
Implementation
AVT uses its proven implementation methodology to implement solutions. The approach can be tailored to suit the exact requirements of each client, and is documented and agreed by all parties at the project initiation.